INYECCIÓN DE ENVASES
(José Zayas García. Dpto. Tecnologías del Envase de ainia)
Introducción.
El moldeo por inyección es uno de los principales métodos de formado de materiales termoplásticos, el cual abarca desde la alimentación del polímero al husillo rotatorio en un cilindro calefactado. Ahí el plástico es fundido y mezclado. El plástico resultante es entonces inyectado a gran presión en un molde cerrado que tiene una o más cavidades de la forma del producto deseado. El molde es enfriado y entonces el plástico solidifica, el molde se abre y las partes son expulsadas.
Unos productos típicos que se obtienen como envases pueden ser contenedores de pared fina, como barquetas, tarrinas, cubos, preformas para soplado, tapones etc.
Debido a los diversos desarrollos en los últimos años, el moldeo por inyección para la industria del envase se ha visto modificada. Los costes de la resina se ha incrementado debido al aumento de los precios del petróleo. La competencia de los envases de papel además de otros procesos se ha intensificado. Para competir eficazmente bajo estas condiciones, el coste de las piezas inyectadas se ha tenido que reducir sin comprometer la vida útil ni la calidad.
Mención especial se puede hacer a los envases multicapa fabricados por el proceso de coinyección. En este caso se utiliza dos inyecctoras suministrando cada una el material de cada capa. Como mayor inconveniente se apunta que es necesario más de una inyectora, siendo esta una maquinaria bastante cara.
Características técnicas principales.
Proceso de inyección
Características principales
Una máquina de inyección consta de tres componentes principales:
1. Unidad de inyección
2. Unidad de cierre
3. Unidad de control
La unidad de inyección plastifica, funde e inyecta la resina a gran temperatura en el molde cerrado. La unidad de cierre soporta las dos mitades del molde, lo cierra y los sujeta fuertemente durante la inyección y finalmente lo abre para expulsar la pieza. La base de la máquina aguanta a las unidades de cierre e inyección y alberga al equipamiento eléctrico, electrónico, neumático e hidráulico necesario para hacer funcionar y controlar la máquina.
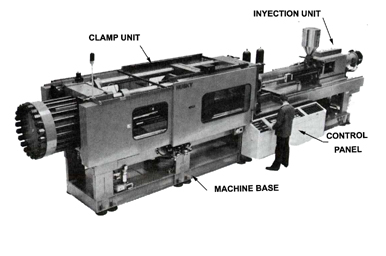
1. La unidad de inyección está conformada por el tornillo y el barril de inyección, la boquilla y las resistencias alrededor del cilindro. El material sólido ingresa por la tolva a la zona de alimentación del tornillo, en esta zona es transportado, por efecto de la rotación del tornillo dentro del cilindro, hacia la zona de fusión donde se plastifica; finalmente el material es bombeado hacia la parte delantera del tornillo en la zona de dosificación. Durante el proceso de plastificación del material el tornillo gira constantemente. Cuando se va a realizar la inyección hacia el molde, el tornillo deja de girar y actúa a manera de pistón, haciendo fluir el plástico fundido hacia el molde y llenando las cavidades. Es bien sabido que la conductividad térmica de los plásticos es muy inferior a la de los metales, por lo que su procesamiento debe hacerse en capas delgadas para que la transferencia de calor sea lo más rápida posible y sostenible económicamente. Esto se logra aprovechando el fenómeno de plastificación, que consiste en la fusión de la capa de material directamente en contacto con la superficie del barril, la cual transmite el calor, por convección forzada, al material sólido en las capas inferiores hasta que se plastifica completamente la masa de material.
Hay dos tipos de unidades de inyección usadas en aplicaciones de envases: de tornillo reciprocante y en dos etapas.
1.1. De tornillo reciprocante: cuando el motor hace girar al husillo, la acción de cizalla sobre el polímero genera la mayor parte del calor necesario para la plastificación. Solo alrededor del 20% del calor requerido es aportado por los calentadores del cilindro. A medida que el husillo gira, retrocede y alimenta el fundido de la parte frontal del husillo. Una vez se alcanza el volumen requerido, deja de girar y se mueve hacia delante para inyectar la resina en el molde. La inyección tiene lugar a una velocidad y presión predeterminadas para asegurar el completo llenado del molde. Una vez el polímero fundido ha sido inyectado, el husillo continúa haciendo presión para mantener la resina dentro del molde bajo presión por un tiempo determinado para compensar la contracción de la pieza mientras se está enfriando en el molde.
1.2. En dos etapas: este tipo de unidades tiene separados los componentes para la plastificación o fusión y la inyección del polímero. La extrusora alimenta de fundido un recipiente de inyección desde el cual el fundido se inyecta en el molde por la acción del pistón de inyección. En el moldeo de pared fina, se debe enfatizar en el diseño de la unidad de inyección, donde debe tener lugar a alta velocidades de inyección, alta presión de inyección y velocidad de plastificación, además de ser reproducible en cada ciclo. La velocidad de inyección es crítica. El polímero fundido que se mueve a través de una cavidad estrecha sobre distancias largas, tiende a enfriar rápidamente y solidifica antes del llenado completo del molde. Para prevenir esto, la velocidad de inyección debe ser muy rápida. Los moldes multicavidad actuales requieren altas velocidad de inyección. Sobre 1.5 kg/s son comunes en el moldeo de piezas de pared estrecha. También se hacen necesarias altas presiones de inyección para alcanzar altas velocidades de inyección en cavidades para piezas de pared estrecha. Presiones de inyección de 200 Mpa se requieren para llenar moldes con polímeros viscosos. Los acumuladores hidráulicos pueden proveer de la fuerza instantánea necesaria para la inyección sin sobredimensionar bombas hidráulicas ni motores. Se necesitan altas velocidades de plastificación con ciclos cortos en aplicaciones para envases.
Una ventaja de las inyectoras de dos etapas es que la extrusora puede funcionar en continuo sin interrupción durante las fases de inyección y mantenimiento.
Es esencial la reproducibilidad de inyección para conseguir alta calidad y mantener el peso de la pieza en el mínimo deseado. Generalmente la exactitud en el control del volumen e inyección en inyectoras de tornillo reciprocante es menor que en la de dos etapas debido a que el tiempo de retardo de la válvula anti-retorno durante la inyección. La reproducibilidad puede ser mejorada usando válvulas de acción rápida con bajas pérdidas hidráulicas y exactos sensores de inyección pistón o cilindro. También, un acumulador dedicado únicamente a la inyección puede asegurar que se almacena el mismo nivel de energía hidráulica y esté preparado para cada inyección. El control de temperatura en la boquilla es fundamental en la definición de las características finales del pieza moldeada, ya que es el último elemento que atravesará el polímero antes de llenar al elemento más importante del sistema de inyección, el MOLDE, que será analizado en su respectiva sección.
2. Unidad de cierre: Consiste de una prensa conformada por dos placas portamoldes, una móvil y otra fija. El sistema de accionamiento de la placa móvil puede ser un mecanismo de palancas acodadas, accionado hidráulicamente, un cilindro hidráulico o un sistema eléctrico de tornillo sinfín accionado por un motor. El parámetro fundamental para dimensionar una unidad de cierre es su fuerza para mantener el molde cerrado. Usualmente se da este valor en toneladas (ton). Otros parámetros importantes en una unidad de cierre son: la distancia mínima entre placas, la distancia máxima de apertura, las dimensiones de las placas y la distancia entre columnas, la carrera del sistema de expulsión. Estos datos se utilizan para dimensionar los moldes.
En la base de la máquina se albergan las unidades de potencia y de control del proceso.
La unidad de potencia: Es el sistema que suministra la potencia necesaria para el funcionamiento de la unidad de inyección y de la unidad de cierre. Los principales tipos de sistemas de potencia se pueden clasificar como:
Sistema de motor eléctrico con unidad reductora de engranajes
Sistema de motor hidráulico con unidad reductora de engranajes
Sistema de potencia eléctrico: El sistema eléctrico se utiliza generalmente en máquinas relativamente pequeñas. Este sistema se emplea tanto para el giro del tornillo como para la apertura y cierre del molde. La máquina emplea dos sistemas mecánicos de engranajes y palancas acodadas, uno para el cierre del molde y otro para el tornillo. Cada uno accionado por un motor eléctrico independiente. El accionamiento del tornillo cuando realiza la inyección lo ejecuta un cilindro hidráulico. En los sistemas con motor eléctrico, la velocidad puede ajustarse sólo en un determinado número de valores, lo cual puede ocasionar problemas en la reproducción de parámetros de operación y dificultar la obtención de piezas con una calidad constante. Los motores eléctricos generan grandes torques de arranque, por lo que debe tenerse precaución al usar tornillos con diámetros pequeños para evitar que se rompan.
Sistema de potencia hidráulico: Los motores hidráulicos son los más comúnmente utilizados, su funcionamiento se basa en la transformación de la potencia hidráulica del fluido en potencia mecánica. A diferencia de los sistemas electromecánicos, donde la potencia es transmitida a través de engranajes y palancas, en un sistema con fluidos estos elementos se sustituyen, parcial o totalmente, por tuberías de conducción que llevan el fluido a presión a los pistones de inyección y de cierre del molde. El fluido que más se utiliza es el aceite debido, principalmente, a sus propiedades lubricantes en aplicaciones que involucran grandes cargas. En los sistemas hidráulicos es común utilizar presiones que varían entre los 70 y 140 kg/cm2. Las ventajas del motor hidráulico con respecto al eléctrico pueden resumirse principalmente en:
· Fácil variación de velocidades, regulando el volumen de fluido.
· La relación entre el torque y la velocidad es aproximadamente lineal. El límite de torque se determina por la presión limitante y el torque de arranque es aproximadamente igual al de funcionamiento.
· Permite arranques y paradas rápidos debido al pequeño momento de inercia.
· Permite relaciones bajas de peso potencia, lo que posibilita alcanzar altas velocidades de inyección del material.
3. Unidad de control: Este sistema básicamente contiene un controlador lógico programable (PLC) y controladores PID para las resistencias eléctricas del cilindro y de la boquilla. El PLC permite programar la secuencia del ciclo de inyección y recibe señales de alarma, por sobrepresión o finales de carrera, para detener el ciclo. Los controladores PID son los más adecuados para el control de temperatura debido a su elevada velocidad de respuesta para mantener la temperatura a los niveles requeridos.
Parámetros de una inyectora
Existen múltiples usos de una máquina de inyección, desde el moldeo de piezas simples hasta la co-inyección (obtención de un producto con dos capas de material distinto) o sobremoldeo, pero los parámetros que las caracterizan son los mismos. Las principales características utilizadas para dimensionar y comparar máquinas inyectoras son:
· Capacidad o fuerza de cierre: usualmente se da en toneladas (ton)
· Capacidad de inyección: es el volumen de material que es capaz de suministrar la máquina en una inyección (cm3/inyección). Es común dar este valor en gramos, tomando como referencia la densidad del poliestireno.
· Presión de inyección: es la presión máxima a la que puede bombear la unidad de inyección el material hacia el molde. Usualmente se trabaja a un 60% de esta presión o menos.
· Capacidad de plastificación: es la cantidad máxima de material que es capaz de suministrar el tornillo, por hora, cuando plastifica el material; se da en kg/h.
· Velocidad de inyección: es la velocidad máxima a la cual puede suministrar la unidad de inyección el material hacia el molde; se da en cm3/s.
Enlaces de interés
|